Crown Victoria Ac Repair Manual
- Ford Crown Victoria Ac System Diagram
- Crown Victoria Ac Repair Manual Download
- Crown Victoria Ac Repair Manual Pdf Free
The Online Ford Crown Victoria Repair Manual by ALLDATA DIY provides specifications, diagrams, diagnostic codes, procedures, OEM part numbers, technical service bulletins, Ford factory recalls for all Ford Crown Victoria systems and components. Results 1 - 48 of 2580 - Haynes Service Repair Manual: Ford Crown Victoria & Mercury Grand. Service information on HVAC, Body & Accessories, Restraints,.
Complete coverage for your Ford Crown Victoria and Mercury Grand Marquis for 1988 thru 2011 (Does not include Mercury Marauder, 5.8L V8 engine information or information specific to natural gas-fueled models):. Routine Maintenance. Tune-up procedures. Engine repair. Cooling and heating. Air Conditioning.
Fuel and exhaust. Emissions control. Ignition. Brakes. Suspension and steering.
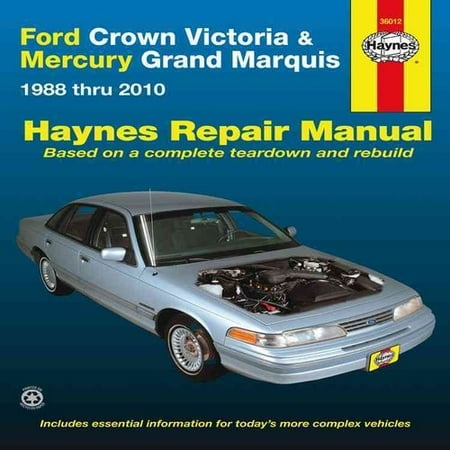
Electrical systems. Wiring diagrams Applications:. 1988-2011 Ford Crown Victoria. 1988-2011 Mercury Grand Marquis.
AC Compressor Operation There are several different compressor designs, but all perform the same function: they move, or pump the refrigerant throughout the system, and they compress the low pressure vaporized refrigerant into a high pressure vapor. Compressors may be of a piston, rotary vane or scroll design. Piston style compressors are the most popular, and are either in line, V-type, radial, axial or wobble plate. The most modern compressors are of a multi-piston design, ranging anywhere from 4 to 10 cylinders.
Some compressors change displacement while operating, and have an effect on refrigerant flow in the system. Most modern compressors have a clutch and drive pulley.
The pulley is belt-driven by one or two V-belts directly from the engine’s crankshaft or by a multi-ribbed V belt or serpentine belt. The pulley turns whenever the engine is running, although the compressor clutch is not engaged when the air conditioning is turned off. Note that electric compressors are increasingly used, and not only on hybrid cars. Some electric compressors are belt-driven as well Read up on the specific system on any vehicle you’re not familiar with before beginning service. These compressors are powered by extremely high voltage, and improper service techniques can result in personal injury.
Special oils are used to keep the internal windings from shorting to the compressor case, and even small contamination with PAG left over in your service equipment is enough to cause total system failure. Only service equipment approved for hybrid/electric compressor service should be used. Compressor Protection Devices. High-Pressure Cutout Switch When certain malfunctions occur, high-side pressures could exceed the safe operating limits of the compressor, hoses, or other components. To prevent this from happening, many systems are equipped with high-pressure cutout switches. These switches open the clutch circuit in the event that pressures become excessive.
This function shuts down the compressor and stops the pressure from climbing higher. This serves two purposes; it protects the compressor from damage, and prevents venting of refrigerant through the pressure relief device (if equipped). Once repairs are made, the switch will allow normal clutch engagement.
High pressure conditions can indicate failures such as a damaged compressor, refrigerant overcharge, condenser restriction, stuck open expansion valve, clogged orifice tube or receiver/drier. Low-Pressure Cutout Switch Some vehicles are equipped with low-pressure cutout switches. The purpose of this switch is also compressor protection. The compressor clutch circuit is opened if the pressure in the system drops too low. This would be an indication that the system has lost some or all of its refrigerant charge. Since the lubricating oil is carried by the refrigerant, a loss could cause damage to the compressor if it were allowed to operate without sufficient lubrication. Low-pressure conditions can indicate failures such as a clogged orifice tube, low refrigerant charge, expansion valve stuck closed, or a restriction in the high side of the A/C system.
Ambient Temperature Switch In non-automatic temperature control systems (ATC), the function of the ambient temperature switch is to inhibit compressor clutch operation in cold ambient temperatures. This sensor opens the electrical path to the compressor clutch when the temperature is below a specified range. This function mainly protects the compressor from poor or no lubrication, which could be the result of cold refrigerant oil. Electronic Compressor Controls Although many of the controls used in automotive air conditioning systems are simple electromechanical switches or other devices, electronic control is now being used, as with engine management and body control computers. Compressor clutch engagement can be determined by the computer when conditions like engine coolant temperature, ambient temperature, throttle position, engine load, etc.
Are optimum for proper system operation. Sensors report on these conditions to the electronic control module (ECM), and the ECM processes this information. If conditions are right, the ECM sends a command to engage the compressor clutch. Conversely, when a problem is detected where conditions are not optimum, the compressor is disengaged by the ECM. Some of the most common sensors that computers use to help them make clutch operation decisions are:. Engine Coolant and Ambient Temperature Sensors These sensors are thermistors, which are resistors whose values change with temperature.
Under cold or hot engine, or cold ambient temperature conditions, compressor clutch engagement may not be desirable. Wide Open Throttle Switch Some vehicles with smaller engines are equipped with a Wide Open Throttle (WOT) switch.
When the accelerator pedal is pressed all the way to the floor, this switch opens the electrical circuit to the compressor clutch to temporarily disable the compressor. This eliminates the load it places on the engine, as it is most often assumed that the pedal on the floor means it is more important to go fast at that moment than to remain cool inside the car. When the accelerator is released from the floor, the compressor clutch will re-enable the compressor. Throttle Position Sensor The throttle position sensor reports to the engine management computer on engine demand conditions.
It works in a capacity like that of the wide open throttle switch. Manifold Absolute Pressure (MAP) And Mass Airflow (MAF) Sensors These are engine load sensors. The computer may decide to prevent clutch operation under conditions of high engine load. Power Steering Pressure Switch This switch is installed in the power steering system and reports on high pressure conditions. High pressure means that there is a load being placed on the engine by the power steering pump.
The computer may decide to temporarily shut down the compressor to prevent engine stalling or low idle speed. It could also raise idle speed through control of an idle speed control device. Drive Belts, Pulleys And Tensioners Squealing noises from the engine compartment that increase in frequency as the engine rpm is raised, or when the A/C compressor is engaged, can usually be attributed to loose belt(s). In addition, pulley misalignment can cause the belt to enter the compressor pulley on an angle, also causing noise. Check the compressor belt(s) for wear and proper adjustment. If replacement is necessary, loosen the belt tensioner or compressor pivot, move the tensioner or compressor to eliminate belt tension, and remove the belt. Never pry the belt from its pulley.
It may be necessary to remove other accessory drive belts to gain access to the compressor belt. Before removing a serpentine V-ribbed belt, make sure there is a belt routing diagram handy or draw one prior to belt removal, to prevent installation problems. Use a socket or wrench to tilt the automatic tensioner away from the belt, and then remove the belt from the pulleys. After the belt is removed, spin the pulley to determine if it wobbles or has any noticeable bearing wear. Inspect the pulleys for chips, nicks, cracks, tool marks, bent sidewalls, severe corrosion or other damage.
Check for hard objects such as small stones or sand that may become imbedded in the bottom of the pulley grooves. When replacing belt(s), inspect the A/C compressor and its corresponding pulley(s) for improper alignment. Aligned pulleys reduce both pulley and belt wear, and vibration of engine components. If the belt pulleys are severely misaligned, look for improper positioning of the A/C compressor or its corresponding pulley, improper fit of the pulley or shaft, or incorrect components installed. Install a new belt by correctly positioning it in its pulley grooves. Using the proper tools, move the compressor to tighten the belt, or in the case of automatically tensioned drives, move the tensioner to a position where the belt can be installed onto the pulleys. Always use manufacturer’s tension recommendations.
Compressor Assembly Knocking noises from the compressor usually indicate internal damage, especially on piston-type compressors. Although technically the compressor can be rebuilt, it is usually replaced.
Always check the compressor mounting and brackets before condemning the compressor for noise. A loose mounting can cause knocking noises from the compressor area that may be mistaken for internal compressor noise. In addition, loose compressor mounting can cause misalignment of the pulleys.To remove the compressor, first recover the refrigerant from the system using the proper equipment.
Disconnect the electrical connectors from the compressor and remove the compressor drive belt. Disconnect the pressure hoses from the compressor and plug the hoses to prevent system contamination. Remove the compressor mounting bolts and lift the compressor from the engine compartment. Drain the compressor of any oil it contained during shipment. Follow the vehicle or compressor manufacturer’s procedure for adding oil to the new or replacement unit. As discussed in the section on lubricants, correct oil levels are critical to system performance and component life. Install the compressor in the engine compartment and secure the mounting bolts.
Be sure to torque the mountings as outlined in the service information to avoid binding the compressor’s internal mechanism. Remove the plugs from the refrigerant hoses and install them onto the compressor assembly, using new seals or 0-rings. Rotate the compressor through by hand at least 20 complete revolutions to thoroughly lubricate the compressor before initial start-up.Install the compressor drive belt and adjust if necessary. Reconnect the electrical connectors. Evacuate and recharge the NC system and check for leaks. Finally, check system performance. Compressor Clutch An electromagnetic clutch provides the mechanical link between the pulley and the compressor input shaft whenever air conditioning is demanded.
The compressor drive hub is usually found at the front of the pulley and is attached directly to the compressor driveshaft. A stationary electromagnetic coil is attached to the face of the compressor, behind the pulley. When current flows through the coil windings, a magnetic field pulls the drive hub snug against the pulley.
Now functioning as a unit, they drive the compressor as long as the coil is energized. Compressor Clutch Inspection Inspect the front of the compressor for oil, which could indicate a leaking front compressor seal.
This would not only cause a refrigerant leak, but the oil could cause the compressor clutch to slip. Connect manifold gauges and make sure there is adequate refrigerant in the system. Start the engine and turn on the A/C. If the compressor clutch does not engage, turn off the engine. Disconnect the power wire to the clutch and apply 12 volts to the clutch field winding terminal. If the clutch engages, then check the power supply to the clutch, including the system protection devices and electronic compressor controls. If the clutch does not engage, then check the clutch ground connection and coil resistance.
If resistance is not within specification, then replace the coil or clutch assembly. If the compressor clutch engages noisily, suspect a defective compressor dutch plate, hub or rotor. Compressor Clutch Replacement Although most compressor clutch and drive pulley components can be serviced in the engine compartment, it is advisable to recover the refrigerant and remove the compressor from the vehicle. After the compressor is removed, clamp it in a suitable holding device with the clutch facing upward. If the clutch plate and hub are fastened to the shaft using a retainer such as a C-clip, remove the clip using the appropriate removal tool. If the clutch plate and hub are fastened to the shaft using a bolt or nut, hold the clutch plate using an appropriate clutch hub holding tool and remove the bolt or nut. After the retainer has been removed, attach a clutch plate and hub puller into the hub assembly.
Turn the center screw of the puller in on the puller body until the clutch plate and hub have been separated from the shaft. Remove the Woodruff key from the hub and place it aside for future use. To remove the clutch rotor assembly, remove the rotor and bearing retaining ring and install the appropriate puller. Hold the puller in place and tighten the puller screw against the guide to remove the pulley rotor and bearing assembly. After the rotor has been removed, inspect it to see if the bearing can be replaced. On some compressors, the bearing and rotor must be replaced as an assembly. However, if the bearing is replaceable, drive the bearing out of the rotor hub with a rotor bearing removal tool.
Jetta won the?Green Car of the World? By mid-2011, almost 10 million Jettas have been produced and sold all over the world. Since then, six generations of this car have been produced and marketed variously as the Atlantic, Fox, Vento, Bora, City Jetta, Jetta City, GLI, Jetta, Clasico, and Sagitar. This car was originally adapted by changing Volkswagen Golf hatchback into a conventional trunk. Since the original version in 1980, the car has grown in size and power with each successive generation.
Next, remove the clutch coil by installing the appropriate puller on the front head of the compressor. Tighten the forcing screw against the puller pilot to remove the coil assembly.
When installing the coil, place the assembly on the front head of the compressor with the terminals in the proper position. Place a suitable installation tool over the opening of the clutch coil housing and align the installer with the compressor front head.
Turn the installation tool forcing screw to force the dutch coil onto the front head until it is properly seated. Make sure the installation tool is properly aligned during installation. Install the bearing into the clutch rotor (if applicable) by placing the rotor on a support. Align the bearing squarely with the hub bore, and using the installation tool, drive the bearing fully into the hub. Now, install the compressor clutch rotor and bearing assembly on the front head. Position a rotor and bearing installation tool directly over the rotor and tighten the center screw to force the assembly onto the compressor front head.
Ford Crown Victoria Ac System Diagram
Make sure the installation tool is properly aligned during installation. Once the assembly is properly seated, install the retainer ring. When installing the replacement clutch and hub, place the Woodruff key into the hub groove.
Make sure that the frictional surfaces of the clutch plate and clutch rotor are free of dirt, oil and debris before installation. Align the shaft keyway with the Woodruff key and place the clutch plate and hub assembly onto the compressor shaft. Do not drive or pound on the clutch hub or shaft. Internal damage to the compressor can result.
Using a clutch plate and hub installation tool, press the hub onto the shaft. Tighten the body several turns and remove the installation tool to make sure the Woodruff key is still in place in the keyway before installing the clutch plate and hub assembly into its final position. After the clutch plate and hub have been seated, compare the air gap between the frictional surfaces with manufacturer’s specifications. If the air gap is sufficient, remove the installation tool, and double-check for proper Woodruff key positioning. If the retainer is a C-clip, install the clip.
If the retainer is a bolt or a nut, hold the clutch and hub with the appropriate tool, and install the bolt or nut. Torque to manufacturer’s specifications. If the compressor clutch components have been replaced with the compressor off the vehicle, reinstall the compressor and connect the pressure lines and electrical connectors.
Evacuate and recharge the A/C system using the proper equipment, and check for leaks. Finally, check system performance. Removing the clutch rotor using a puller. Removing the bearing from the clutch rotor. Measuring the clearance between the compressor clutch friction surfaces.
Ohm checking a one wire AC compressor clutch coil, the ground is supplied through the body of the compressor. Two types of high-pressure cutout switches. The single function switch interrupts compressor function if system pressure becomes too high. The dual function switch first engages the high-speed cooling fan in an attempt to lower pressure by increasing heat transfer at the condenser.
However, if system pressure continues to rise after the fan has been engaged, then the switch will interrupt compressor operation. Holding the clutch hub with a suitable tool while the bolt or nut is removed. Removing the clutch plate and hub using a puller.
A typical AC compressor removal and installation diagram. Exploded view of the AC compressor clutch with individual components labeled. This post was written by: Martin Hand Donations If you find this information helpful please consider a donation. These articles, questions and comments are very time consuming so even a small donation gives me motivation to keep educating automotive owners.
Donations will allow us to continue open questioning/comments, automotive education and repair tutorials in the future as the business grows. All proceeds go to the expansion and maintenance mdhmotors.com. About Martin Hand ASE Certified L1 Advanced Mastertech. Martin Hand has over 15 years experience in Asian and European Import Auto Repair. Specializing in electrical diagnosis, engine performance, AT/MT transmission repair/rebuild. Martin is also pursuing a degree in Computers Science & Information Systems starting at Portland Community College while he plans to transfer to OIT.
Crown Victoria Ac Repair Manual Download
Certified in Java application level programming, experienced with other languages such as PHP, Ruby, JavaScript and Swift. Martin has future plans of automotive diagnostic software development. Yes, I agree with you on this point that the designs of compressor vary from one another; however their purposes are same. The compressor helps to move liquid refrigerant around in a pipe.
Crown Victoria Ac Repair Manual Pdf Free
If the compressor of your car AC does not function well, the worth of having the AC will go in vain. So, you should take your vehicle to a well known garage well ahead of the hot summer. The mechanics employed there check your vehicle and fix the issues if it has. If everything is OK, then he only suggests you how to take care of your vehicle effectively.